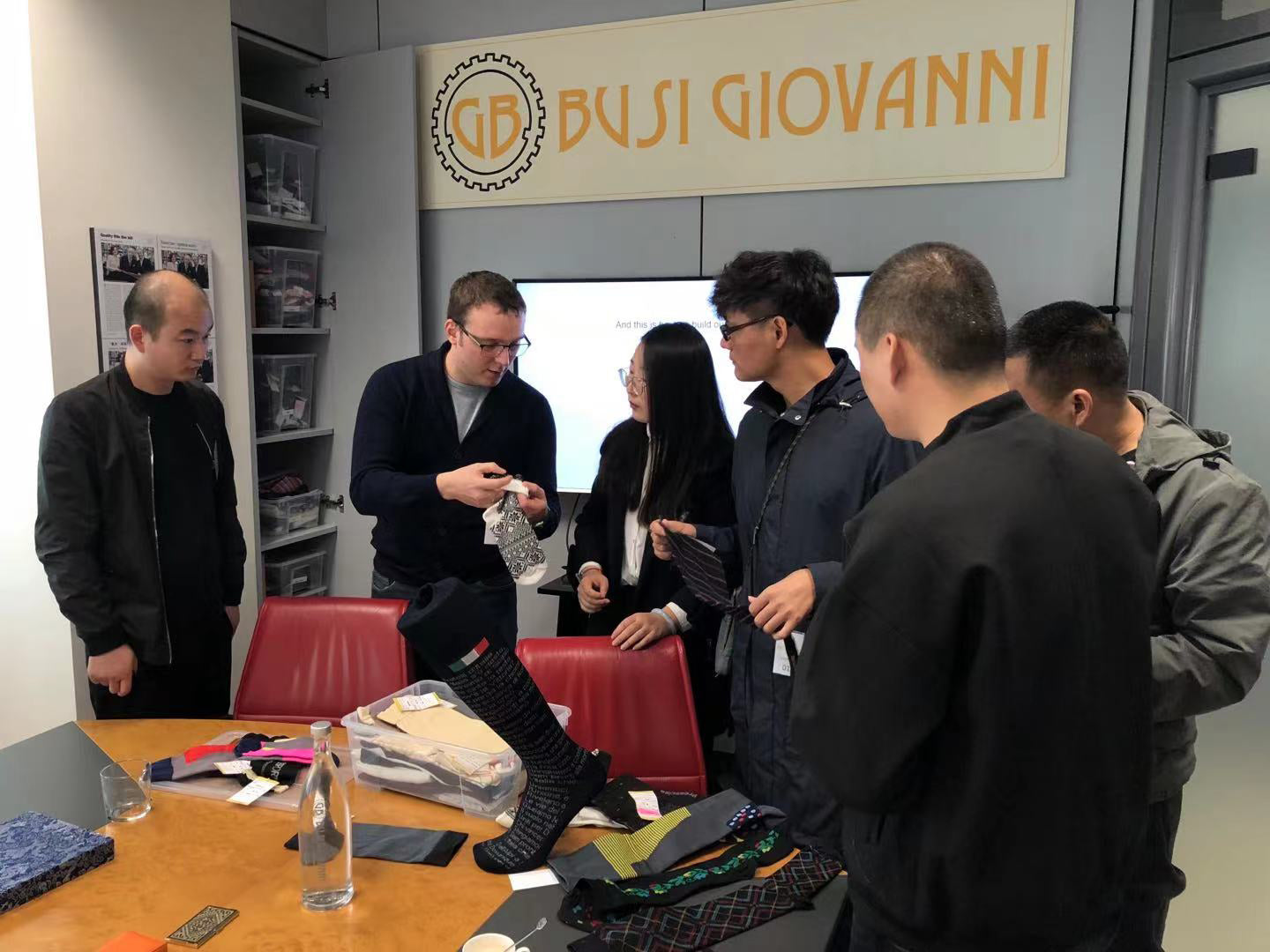
The Craftsmanship Of Socks
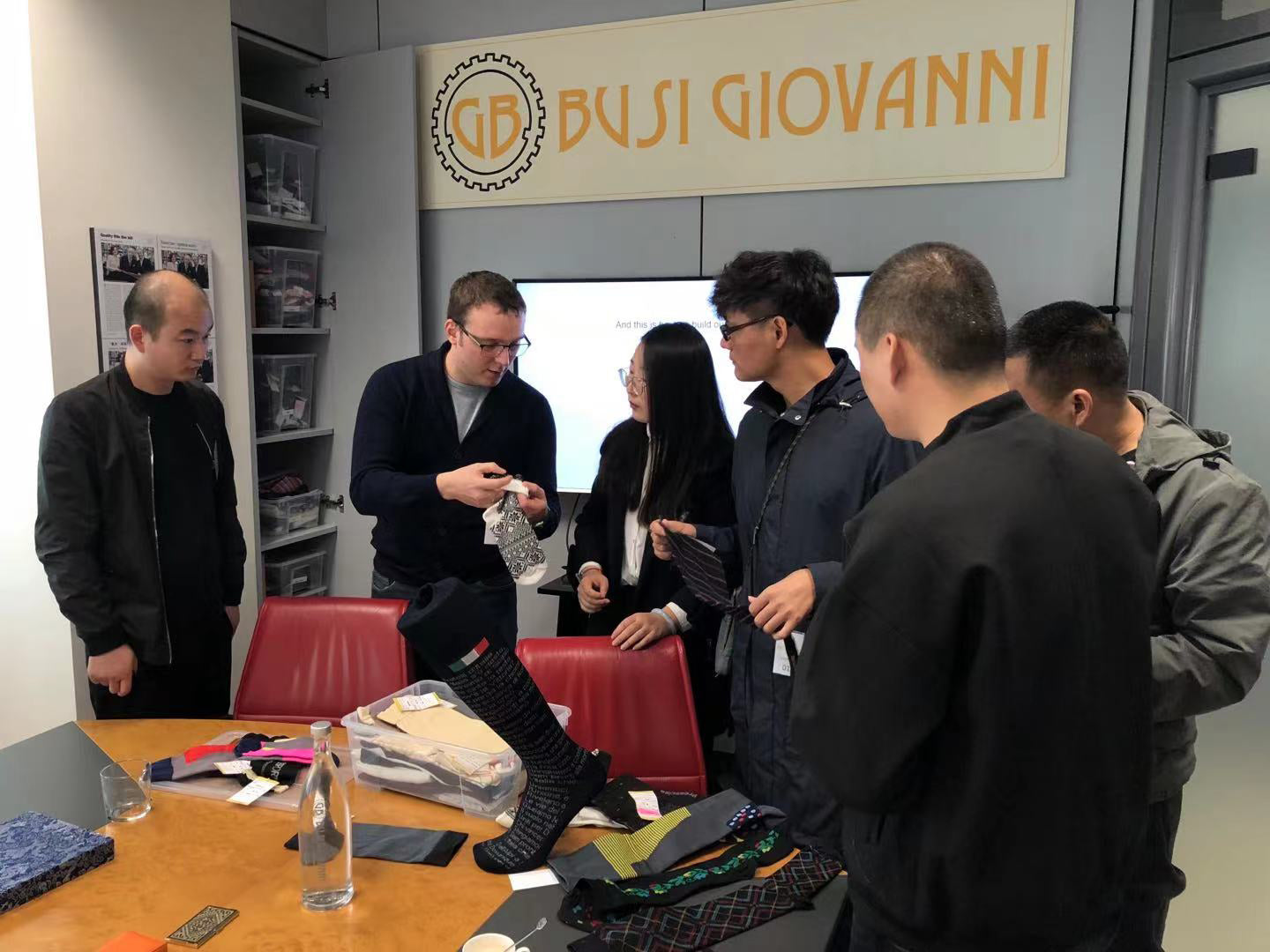
- Professionalism, innovation, craftsmanship, refinement and uniqueness are our strengths. We have the most expensive BUSI sock machine in the world.
- Technicians have traveled to the Hermès production factory in Italy many times to learn, and have gone deep into the production workshops of international first-line big brands to learn and master the craftsmanship of Italian craftsmen.
- After five years of upgrading and improvement, it has become the first domestic brand and the only one with the top 240-needle high-density sock machine and advanced technology imported from Italy.
- The company adheres to the concept of "Make steps for next" and insists on people-oriented sustainable development. The founder Mr. Chen once said frankly that in the face of fierce market competition, he insisted on being a person who sticks to his vision.
85% of the raw materials are imported from Italy and have their own texture and luster.
The raw material of the socks is 60-100 count singed mercerized cotton and the heels are reinforced with nylon and there is no spandex process.This makes the socks very light and breathable, creates a sense of layering, and improves the wear resistance of the socks and extends the service life of the socks.
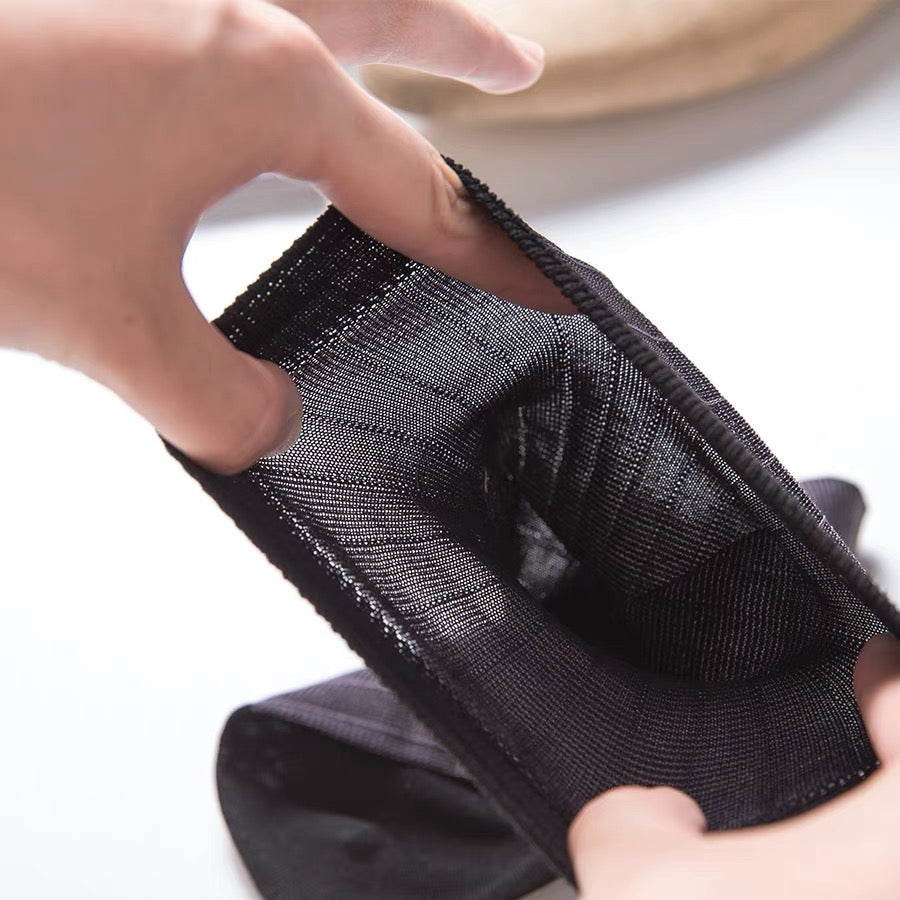
- The hallmark of high-quality socks is that they are made in one piece.
- Seamless socks don't have bulky toe seams that can cause damage to the skin and lead to blisters and skin irritation, and as the name implies, seamless socks are socks without seams.
- While some seamless socks may actually have a slight, invisible seam, they won’t cause irritation and discomfort like regular socks.
- Seamless socks are also perfect for guests who may suffer from sensitive skin or have sensory issues.
Like every revolutionary brand, Tomoz Echo always pursues high quality.
Through 240-needle extreme craftsmanship, non-sensitive Lycra thread reinforcement, no traditional yarn covering process, single and double needles can be switched freely, and high-precision craftsmanship, pairs of cotton socks with a texture like stockings are produced.
Our 7 steps
1. According to the needs of customers, communicate accurately and the designer will design.
2. Select matching raw materials for machine proofing.
3. Confirm the sample process and raw materials again.
4. Confirm the production quantity and delivery time:
① 3-7 days for spot;
② 15 days for the customization cycle of conventional raw materials;
③ 30 days for the customization cycle of special raw materials (ultra-fine 80-count Merino wool).
5. Machine production:
& Knitting: BUSI sock machine 240 needles;
& Sewing: BUSI sock machine boneless socks one-piece sewing;
& Dedicated quality inspection and follow-up: dedicated personnel are responsible for timely grasping the production situation;
& Shaping: high-pressure automatic 240-piece automatic shaping machine, computer settings for different socks with different temperatures and drying times;
& Packaging matching: two manual processes for packaging, quality inspection of each pair of socks.
6. Product packaging: a variety of packaging methods are available (our retail products are packaged in international organic cotton recycling storage bags, which are recyclable without OPP).
7. Delivery: Various logistics delivery modes meet the requirements of different customers.
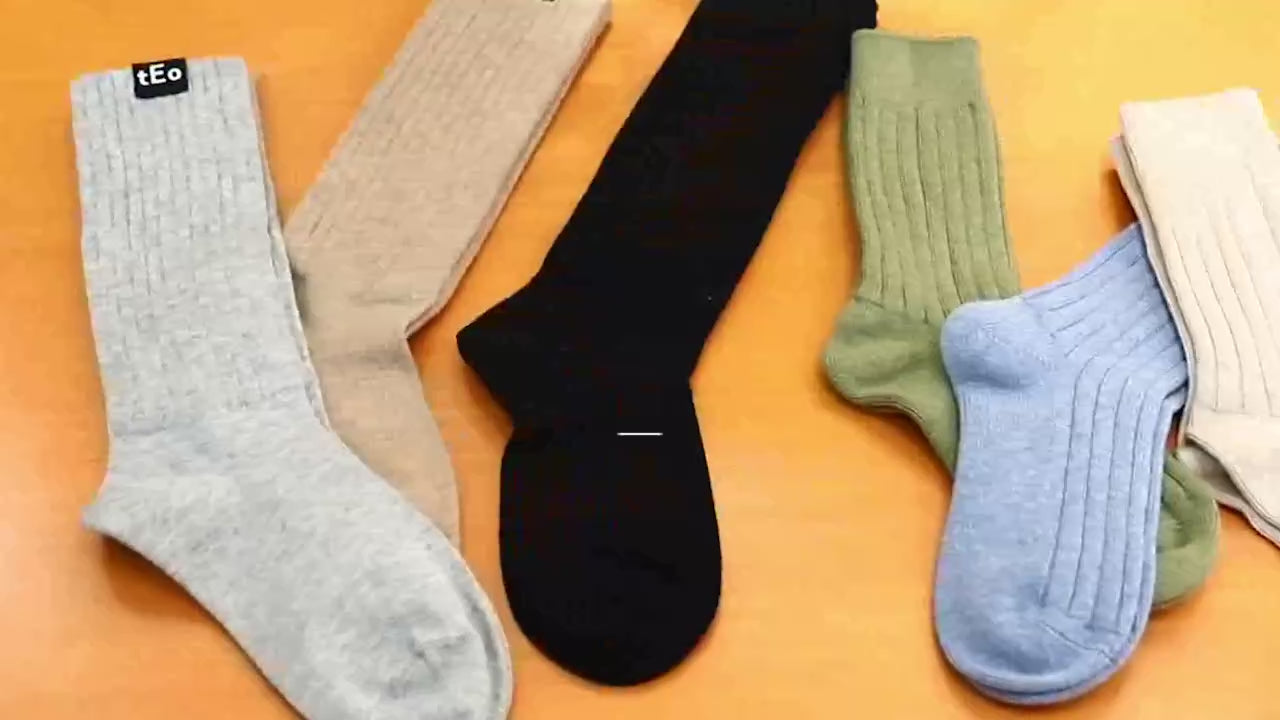